RELIABILITY SERVICES
.avif)
Official partnership
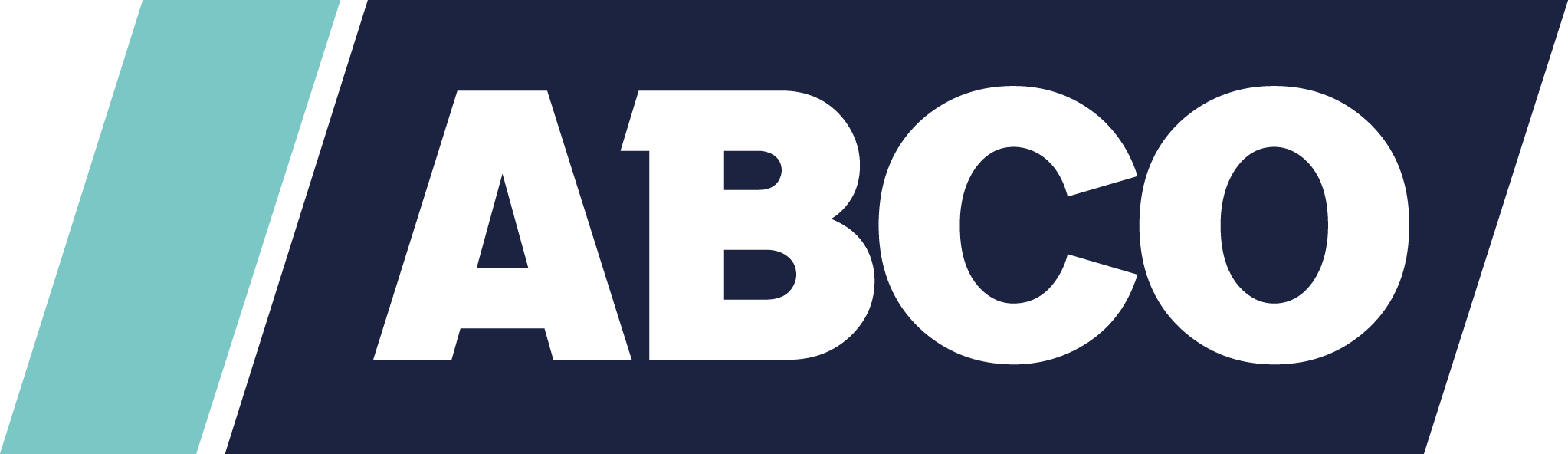
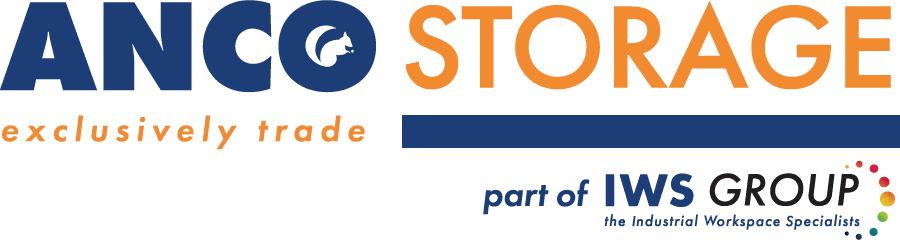
Official partnership
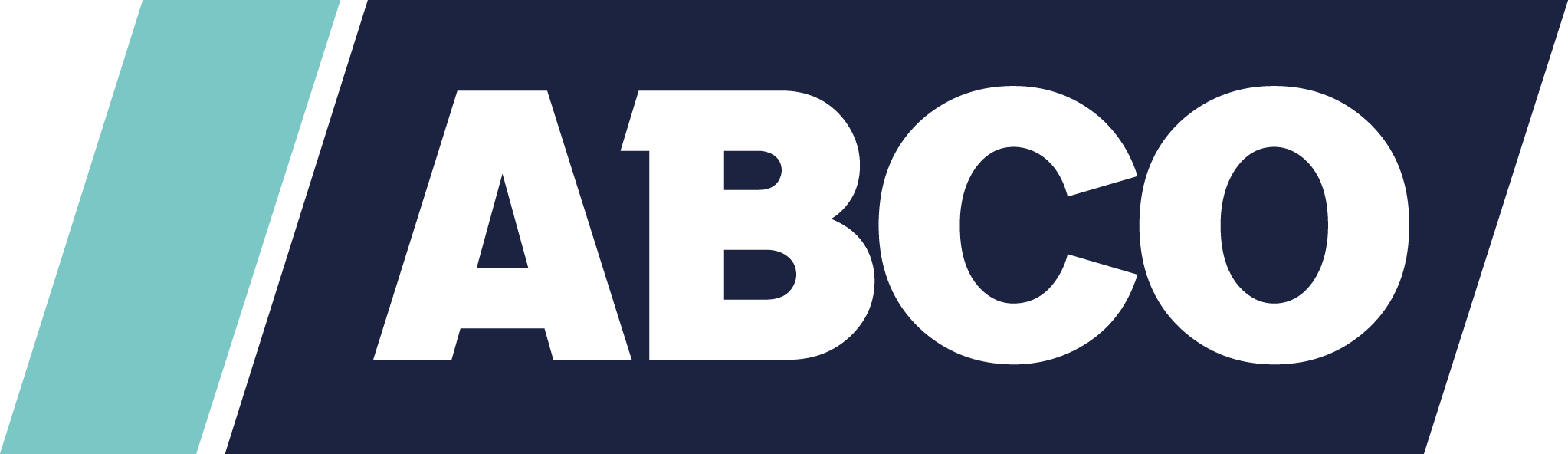
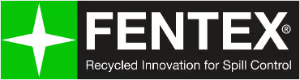
Services aligned to your sustainability agenda
Our reliability services are designed to support your sustainability agenda. Whether you’re working towards net zero emissions, or focusing on extending the operational life of your systems to promote circular economics, we are able to devise a program of services that perfectly align with your environmental goals.
.avif)
.avif)
Spill control solutions
Find out all the ways that our reliability services can help you ensure your business is future-ready.
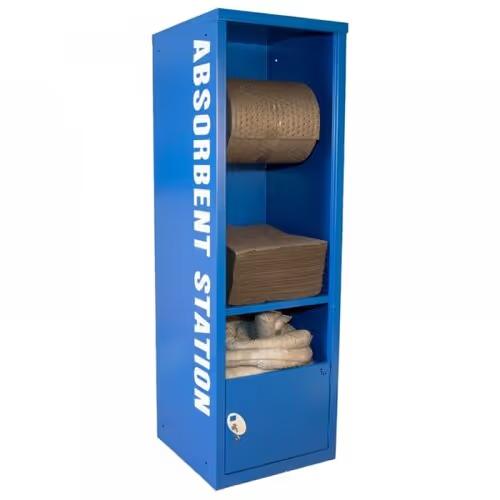
Absorbent stations
Fast access to multiple absorbents for the reactive management of small spills and leakages. These self-contained steel units centralise wiping, cleaning and absorption, reducing the need to use an emergency spill kit for minor incidents.
- Absorbent pads for spills and leakages
- Absorbent roll for wiping and cleaning
- Absorbent socks to contain larger spills
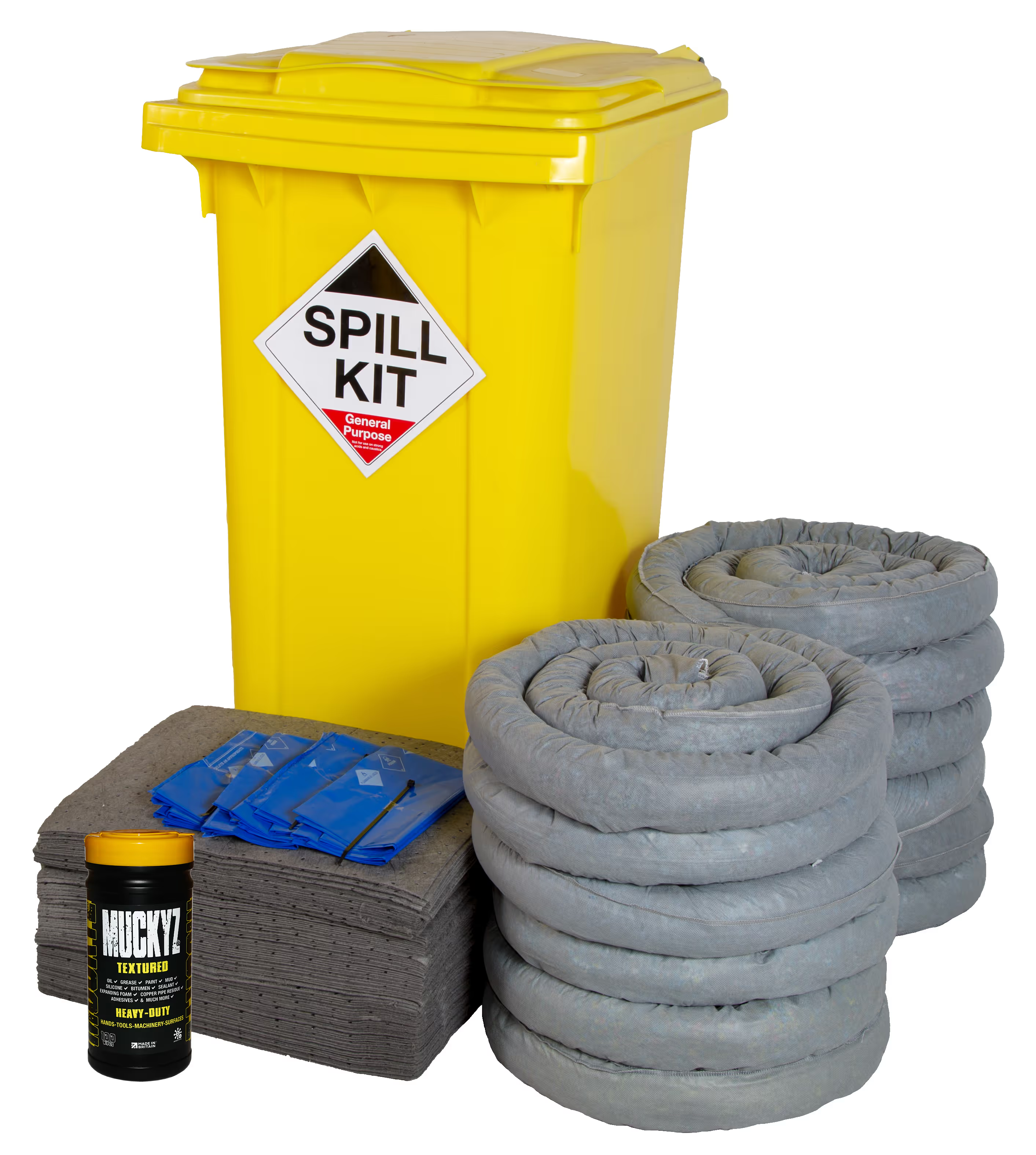
Emergency spill kits
Spill kits range from 15l to 1100l in capacity, and are specified according to the liquids in use. They are sealed with a breakable tag to indicate when they have been used for an emergency situation.
- General purpose spill kits for non-hazardous spills
- Oil and fuel spill kits for machinery or vehicle emergencies
- Chemical spill kits for hazardous chemicals
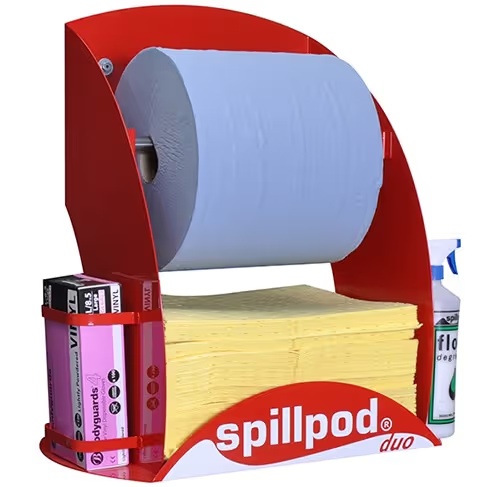
Spillpod®
Wall mounted for workshop environments, these self-contained steel units hold multiple absorbents, disposable gloves and floor degreaser.
- Spillpod pads are eight times more absorbent than rags
- Perforated paper roll for general cleaning and wiping
- Available for general purpose, oil and fuel or chemical absorption
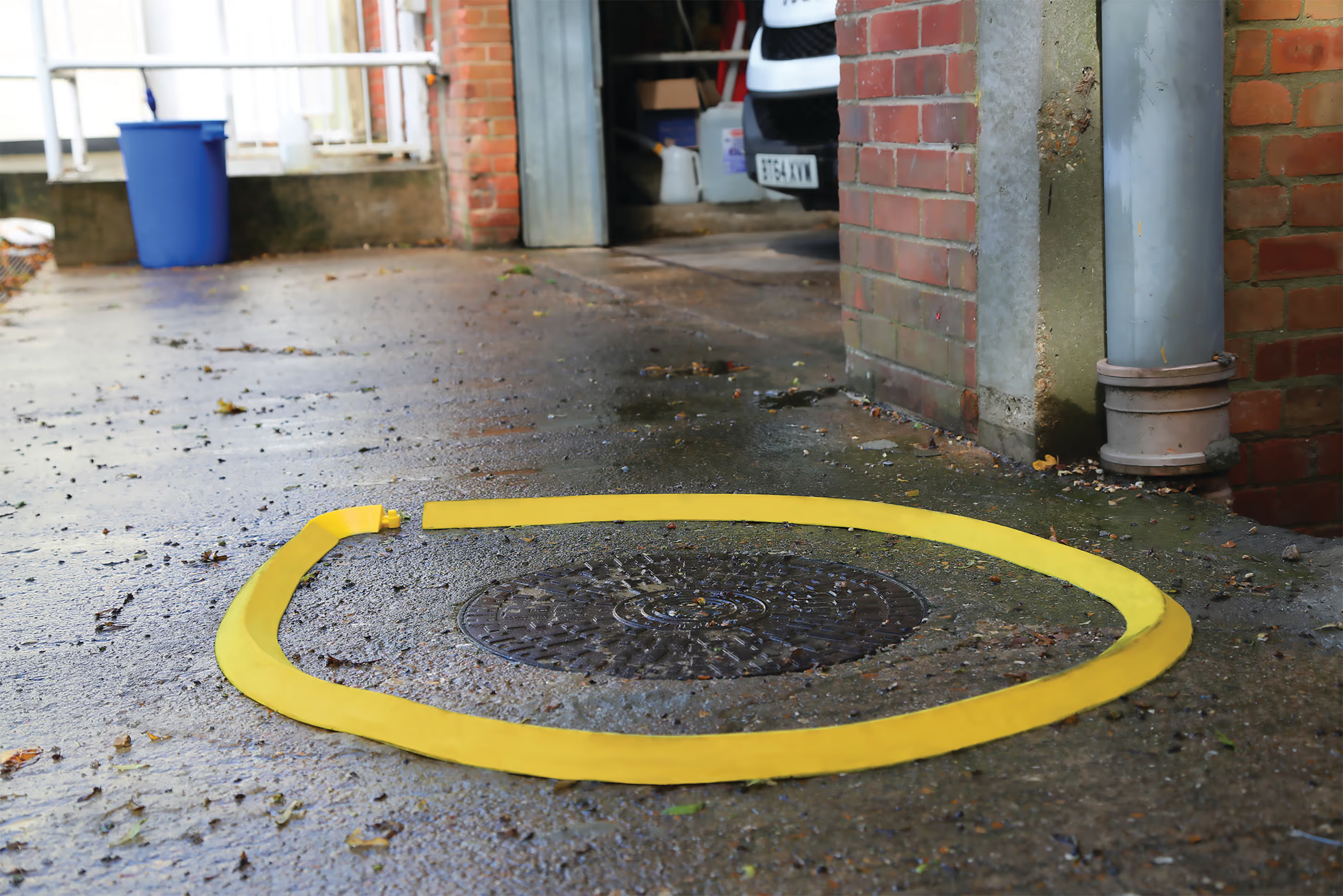
Drain protection
A critical part of environmental protection during a spill emergency is having suitable drain protection, which could include land booms, drain booms, drain blockers and drain filters.
- Heavy-weight drain covers protect against hazardous spills
- Spill berms to contain and divert spills away from the drain
- Neoprene drain covers for reusable, easy to clean protection
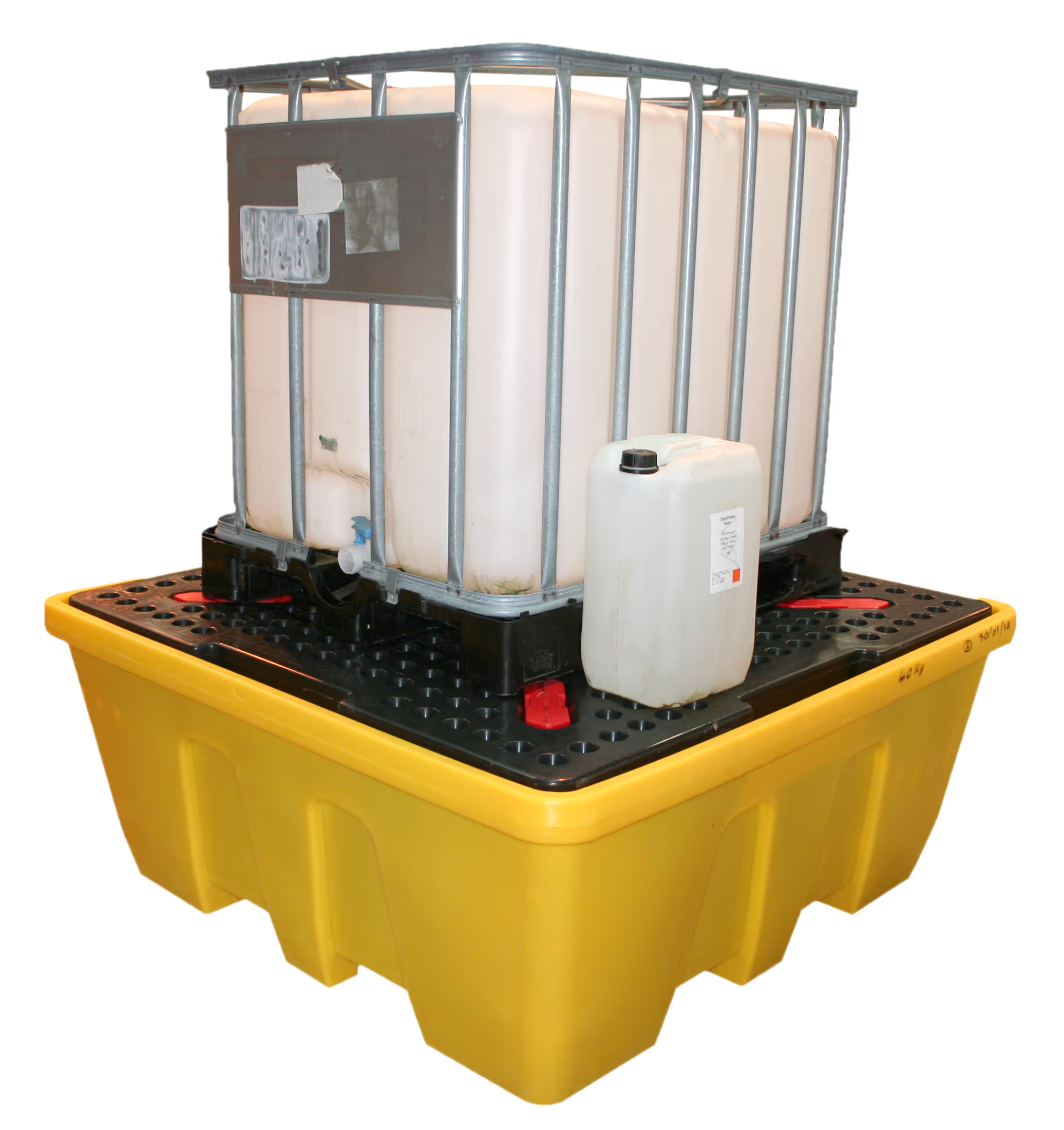
Containment
Containment solutions prevent ground contamination during drum decanting, filling tasks and in the event of a leak, drip or spill. Our spill containment products are 100% recyclable and compliant with UK Oil Storage Regulations.
- Drip pans and trays to catch leaks and drips
- Spill pallets and IBC bunds compliant with Oil Storage Regulations
- Portable trays and bunds for projects or adhoc tasks
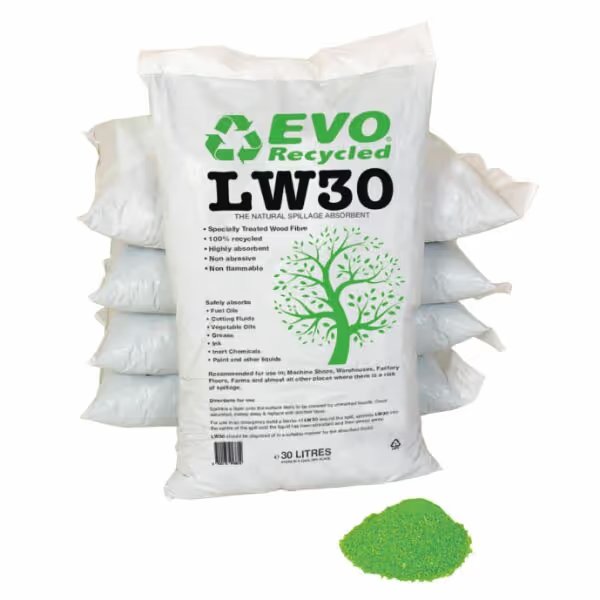
Loose absorbents
Ideal for industrial spillages and general clean-up duties, this 100% recycled wood fibre or gypsum particulates are fireproof, lightweight and safe to use.
- EVO Recycled LW30 absorbs fuel oils, cutting fluids, grease, inert chemicals, paint and other liquids
- EVO DRI absorbent granules for spills and leaks of non-hazardous fluids
.avif)
Learn more about Reliability Services
Find out all the ways that our reliability services can help you ensure your business is future-ready.
Preventative maintenance
Working with our major brand manufacturing partners, we are best placed to implement both manual and digital data-driven component, system-specific and whole asset preventative maintenance.
.avif)
Air leak surveys
We can support your engineers in identifying and correcting neglected air leaks in compressor systems. In doing so, we are able to prevent breakdowns, save energy and drive cost efficiencies.
.webp)
Specification upgrades
Using our broad product portfolio, we are able to identify areas of improvement throughout your facility, and recommend specification upgrades that will directly result in cost or energy savings, better operational performance and less downtime.
.webp)
Uptime surveys
Combining a range of our value added services, these surveys take a whole-facility approach to improving uptime. Our recommendations cover all aspects of operation, maintenance and energy usage, and can be tailored to meet specific objectives or to align with your sustainability agenda.
.webp)
Prevent component obsolescence, promote circularity
Extending the operational life of machinery and systems reduces customer reliance on finite materials in line with circular economic principles. By identifying alternatives for obsolete parts, we are able to prevent whole-machine replacements, preserving environmental systems and often improving operational efficiencies at the same time.
.webp)
Popular racking solutions
.avif)
Heavy Rivet Racking
Store products of varying weights and dimensions within a single rigid industrial rivet racking system.
- Vast range of bay sizes
- Suitable for heavy and bulky items
- Compatible with J Rivet Racking for a combination system
- Max shelf load: 400-600kg UDL
- Max bay load: 2800kg UDL
.avif)
J Rivet Racking
Access products or storage bins easily with a racking system that optimises space by minimising the racking frame.
- Vast range of bay sizes
- Highly flexible configurations
- Compatible with Heavy Rivet Racking for a combination system
- Max shelf load: 150kg UDL
- Max bay load: 2800kg UDL
.avif)
Pallet Racking
Store pallets easily with a racking system optimised according to product type, throughput and warehouse equipment.
- Range of systems to suit different goods and storage needs
- Optimal use of floor space
- Designed for speed of throughput and warehouse equipment
- Highly configurable
- Max beam load: 3790kg (UDL)
.avif)
Tilt bins
Store fasteners and fixings so they are easy to identify, access and replenish, either lineside or in engineering stores.
- Protects stock from dirt and dust
- Store, view and retrieve and restock easily
- Drawers tip open for easy access
- Available in four bin sizes
- Configurable to suit different storage needs
.avif)
Kanban Shelving
Simplify stock rotation and replenishment with rivet racking kanban systems either lineside or in your engineering stores.
- Sloped shelving offers easy access for operatives
- Can increase production efficiency in manufacturing
- Ideal for inventory management
- Can be installed in banks for more shelving space
- Max shelf load: 80kg (UDL)
.avif)
Trays and bins
Store products safely, improve inventory management and provide quick access to engineering essentials.
- Wide range of rhino bins and shelf trays
- Shock proof plastic construction
- Options for mild, mid or heavy duty industrial applications
- Stackable or hanging options
- Contents are easily stored, identified, picked and replenished
OUR PROCESS
.avif)
1) Needs assessment
Meet with our in-house specialists to discuss the needs of your team and the space you have available for your workshop.
.avif)
2) Bespoke workshop proposal
Understand which combination of solutions will best fulfill the needs of your engineers and your operations.
.avif)
3) Installation
Your bespoke workshop, installed to the highest standards by our inhouse installation experts, with the support of our manufacturing partner Beta.
.avif)
4) Ongoing management
Replenishment of tools, consumables and the management of your stores and spares to your team always have access to the items they need.
Learn more about Reliability Services
Find out all the ways that our reliability services can help you ensure your business is future-ready.
Seirei
Sort
Working with our major brand manufacturing partners, we are best placed to implement both manual and digital data-driven component, system-specific and whole asset preventative maintenance.
Seiton
Set in order
We can support your engineers in identifying and correcting neglected air leaks in compressor systems. In doing so, we are able to prevent breakdowns, save energy and drive cost efficiencies.
Seiso
Shine
Using our broad product portfolio, we are able to identify areas of improvement throughout your facility, and recommend specification upgrades that will directly result in cost or energy savings, better operational performance and less downtime.
Seiketsu
Standardise
Combining a range of our value added services, these surveys take a whole-facility approach to improving uptime. Our recommendations cover all aspects of operation, maintenance and energy usage, and can be tailored to meet specific objectives or to align with your sustainability agenda.
Shitsuke
Sustain
Extending the operational life of machinery and systems reduces customer reliance on finite materials in line with circular economic principles. By identifying alternatives for obsolete parts, we are able to prevent whole-machine replacements, preserving environmental systems and often improving operational efficiencies at the same time.
.avif)
.webp)
Our stock management and inventory control solutions
.jpg)
ABCO SelfSCAN™
This digital solution enables store managers or engineers to scan stock bins and submit an order via a fully-customised app, quickly at the point of use.
.jpg)
ABCO StockSCAN™
An ABCO team visits regularly to provide a complete end-to-end service. Inventory is fully managed with quality reporting and a significant time saving for busy engineers.
.jpg)
ABCO StockCOUNTER™
An ABCO trade counter onsite with a full time team working from your premises. This dedicated service, supports your engineers with the full backing of ABCO’s operations.
.jpg)
ABCO StockVEND™
Fully configured vending machines, managed and stocked by ABCO, to provide around the clock access to engineering essentials, mechanical spares and PPE.
Learn more about Reliability Services
Find out all the ways that our reliability services can help you ensure your business is future-ready.
Preventative maintenance
Working with our major brand manufacturing partners, we are best placed to implement both manual and digital data-driven component, system-specific and whole asset preventative maintenance.
.avif)
Air leak surveys
We can support your engineers in identifying and correcting neglected air leaks in compressor systems. In doing so, we are able to prevent breakdowns, save energy and drive cost efficiencies.
.webp)
Specification upgrades
Using our broad product portfolio, we are able to identify areas of improvement throughout your facility, and recommend specification upgrades that will directly result in cost or energy savings, better operational performance and less downtime.
.webp)
Uptime surveys
Combining a range of our value added services, these surveys take a whole-facility approach to improving uptime. Our recommendations cover all aspects of operation, maintenance and energy usage, and can be tailored to meet specific objectives or to align with your sustainability agenda.
.webp)
Prevent component obsolescence, promote circularity
Extending the operational life of machinery and systems reduces customer reliance on finite materials in line with circular economic principles. By identifying alternatives for obsolete parts, we are able to prevent whole-machine replacements, preserving environmental systems and often improving operational efficiencies at the same time.
.webp)
.avif)
Air leak surveys
Customer: Tin can manufacturer
Challenge: Customer wanted to identify neglected air leaks on an ongoing basis.
Solution: Working alongside our manufacturing partner, we conducted air leak surveys throughout the customer’s site. Going one step further, we then trained the onsite engineers to conduct future air leak surveys themselves. This solution delivered a 17% reduction in compressed air usage, a monthly energy saving of £14,000 and the elimination of outsourcing costs for future air leak surveys.
.webp)
.webp)
Air leak surveys
Customer: Tin can manufacturer
Challenge: Customer wanted to identify neglected air leaks on an ongoing basis.
Solution: Working alongside our manufacturing partner, we conducted air leak surveys throughout the customer’s site. Going one step further, we then trained the onsite engineers to conduct future air leak surveys themselves. This solution delivered a 17% reduction in compressed air usage, a monthly energy saving of £14,000 and the elimination of outsourcing costs for future air leak surveys.
Air leak surveys
Customer: Tin can manufacturer
Challenge: Customer wanted to identify neglected air leaks on an ongoing basis.
Solution: Working alongside our manufacturing partner, we conducted air leak surveys throughout the customer’s site. Going one step further, we then trained the onsite engineers to conduct future air leak surveys themselves. This solution delivered a 17% reduction in compressed air usage, a monthly energy saving of £14,000 and the elimination of outsourcing costs for future air leak surveys.
.webp)
Air leak surveys
Customer: Tin can manufacturer
Challenge: Customer wanted to identify neglected air leaks on an ongoing basis.
Solution: Working alongside our manufacturing partner, we conducted air leak surveys throughout the customer’s site. Going one step further, we then trained the onsite engineers to conduct future air leak surveys themselves. This solution delivered a 17% reduction in compressed air usage, a monthly energy saving of £14,000 and the elimination of outsourcing costs for future air leak surveys.
Air leak surveys
Customer: Tin can manufacturer
Challenge: Customer wanted to identify neglected air leaks on an ongoing basis.
Solution: Working alongside our manufacturing partner, we conducted air leak surveys throughout the customer’s site. Going one step further, we then trained the onsite engineers to conduct future air leak surveys themselves. This solution delivered a 17% reduction in compressed air usage, a monthly energy saving of £14,000 and the elimination of outsourcing costs for future air leak surveys.
.webp)
Air leak surveys
Customer: Tin can manufacturer
Challenge: Customer wanted to identify neglected air leaks on an ongoing basis.
Solution: Working alongside our manufacturing partner, we conducted air leak surveys throughout the customer’s site. Going one step further, we then trained the onsite engineers to conduct future air leak surveys themselves. This solution delivered a 17% reduction in compressed air usage, a monthly energy saving of £14,000 and the elimination of outsourcing costs for future air leak surveys.
Customer: Tin can manufacturer
Challenge: Customer wanted to identify neglected air leaks on an ongoing basis.
Solution: Working alongside our manufacturing partner, we conducted air leak surveys throughout the customer’s site. Going one step further, we then trained the onsite engineers to conduct future air leak surveys themselves. This solution delivered a 17% reduction in compressed air usage, a monthly energy saving of £14,000 and the elimination of outsourcing costs for future air leak surveys.
%20(2).avif)
Air leak surveys
Customer: Tin can manufacturer
Challenge: Customer wanted to identify neglected air leaks on an ongoing basis.
Solution: Working alongside our manufacturing partner, we conducted air leak surveys throughout the customer’s site. Going one step further, we then trained the onsite engineers to conduct future air leak surveys themselves. This solution delivered a 17% reduction in compressed air usage, a monthly energy saving of £14,000 and the elimination of outsourcing costs for future air leak surveys.
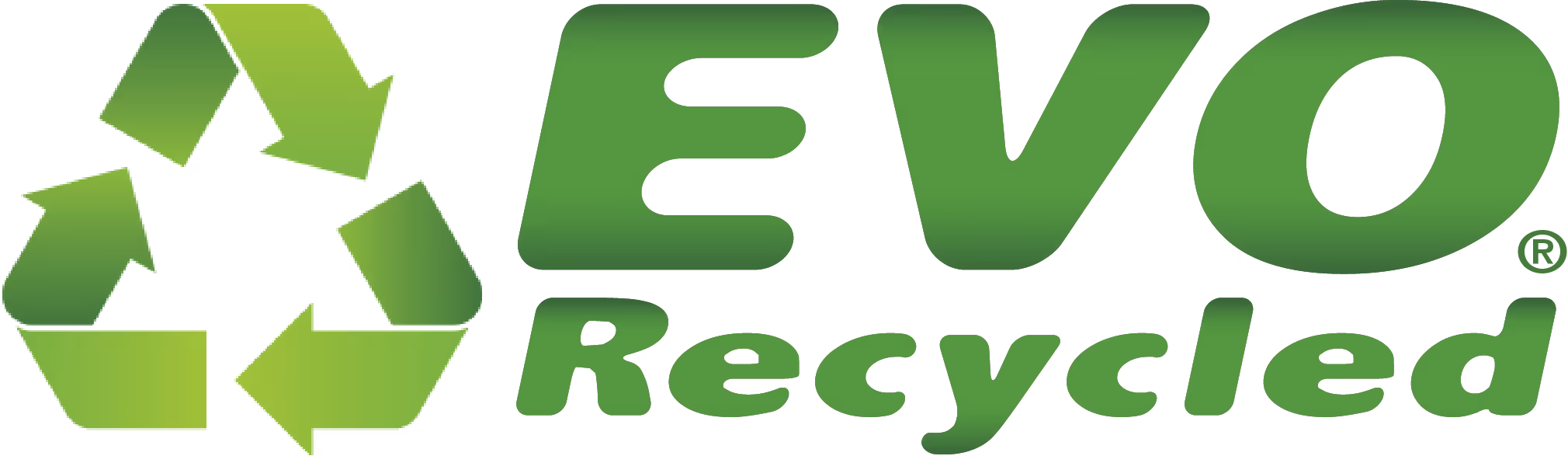
The EVO Recycled® range includes:
- Absorbent pads and rolls
- Absorbent socks and cushions
- Emergency spill kits
- Absorbent stations and Spillpods
- Loose absorbents
- Drip trays, spill trays and spill pallets
Learn more about Reliability Services
Find out all the ways that our reliability services can help you ensure your business is future-ready.
Preventative maintenance
Working with our major brand manufacturing partners, we are best placed to implement both manual and digital data-driven component, system-specific and whole asset preventative maintenance.
.avif)
Air leak surveys
We can support your engineers in identifying and correcting neglected air leaks in compressor systems. In doing so, we are able to prevent breakdowns, save energy and drive cost efficiencies.
.webp)
Specification upgrades
Using our broad product portfolio, we are able to identify areas of improvement throughout your facility, and recommend specification upgrades that will directly result in cost or energy savings, better operational performance and less downtime.
.webp)
Uptime surveys
Combining a range of our value added services, these surveys take a whole-facility approach to improving uptime. Our recommendations cover all aspects of operation, maintenance and energy usage, and can be tailored to meet specific objectives or to align with your sustainability agenda.
.webp)
Prevent component obsolescence, promote circularity
Extending the operational life of machinery and systems reduces customer reliance on finite materials in line with circular economic principles. By identifying alternatives for obsolete parts, we are able to prevent whole-machine replacements, preserving environmental systems and often improving operational efficiencies at the same time.
.webp)
.avif)
Preventing component obsolescence to promote circularity
Customer: Global construction company
Challenge: Critical sand casting machine threatened by component obsolescence
Solution: Working with a manufacturing partner, we identified replacements for obsolete electrical components. By keeping the sand casting machine in service longer, we reduced the customer’s reliance on finite materials, and preserved environmental ecosystems in line with their circularity agenda.
.webp)
.webp)
.webp)
Preventing component obsolescence to promote circularity
Customer: Global construction company
Challenge: Critical sand casting machine threatened by component obsolescence
Solution: Working with a manufacturing partner, we identified replacements for obsolete electrical components. By keeping the sand casting machine in service longer, we reduced the customer’s reliance on finite materials, and preserved environmental ecosystems in line with their circularity agenda.
Preventing component obsolescence to promote circularity
Customer: Global construction company
Challenge: Critical sand casting machine threatened by component obsolescence
Solution: Working with a manufacturing partner, we identified replacements for obsolete electrical components. By keeping the sand casting machine in service longer, we reduced the customer’s reliance on finite materials, and preserved environmental ecosystems in line with their circularity agenda.
.webp)
Preventing component obsolescence to promote circularity
Customer: Global construction company
Challenge: Critical sand casting machine threatened by component obsolescence
Solution: Working with a manufacturing partner, we identified replacements for obsolete electrical components. By keeping the sand casting machine in service longer, we reduced the customer’s reliance on finite materials, and preserved environmental ecosystems in line with their circularity agenda.
Preventing component obsolescence to promote circularity
Customer: Global construction company
Challenge: Critical sand casting machine threatened by component obsolescence
Solution: Working with a manufacturing partner, we identified replacements for obsolete electrical components. By keeping the sand casting machine in service longer, we reduced the customer’s reliance on finite materials, and preserved environmental ecosystems in line with their circularity agenda.
.webp)
Preventing component obsolescence to promote circularity
Customer: Global construction company
Challenge: Critical sand casting machine threatened by component obsolescence
Solution: Working with a manufacturing partner, we identified replacements for obsolete electrical components. By keeping the sand casting machine in service longer, we reduced the customer’s reliance on finite materials, and preserved environmental ecosystems in line with their circularity agenda.
Customer: Global construction company
Challenge: Critical sand casting machine threatened by component obsolescence
Solution: Working with a manufacturing partner, we identified replacements for obsolete electrical components. By keeping the sand casting machine in service longer, we reduced the customer’s reliance on finite materials, and preserved environmental ecosystems in line with their circularity agenda.
Learn more about Reliability Services
Find out all the ways that our reliability services can help you ensure your business is future-ready.
Preventative maintenance
Working with our major brand manufacturing partners, we are best placed to implement both manual and digital data-driven component, system-specific and whole asset preventative maintenance.
.avif)
Air leak surveys
We can support your engineers in identifying and correcting neglected air leaks in compressor systems. In doing so, we are able to prevent breakdowns, save energy and drive cost efficiencies.
.webp)
Specification upgrades
Using our broad product portfolio, we are able to identify areas of improvement throughout your facility, and recommend specification upgrades that will directly result in cost or energy savings, better operational performance and less downtime.
.webp)
Uptime surveys
Combining a range of our value added services, these surveys take a whole-facility approach to improving uptime. Our recommendations cover all aspects of operation, maintenance and energy usage, and can be tailored to meet specific objectives or to align with your sustainability agenda.
.webp)
Prevent component obsolescence, promote circularity
Extending the operational life of machinery and systems reduces customer reliance on finite materials in line with circular economic principles. By identifying alternatives for obsolete parts, we are able to prevent whole-machine replacements, preserving environmental systems and often improving operational efficiencies at the same time.
.webp)
.avif)
Preventative maintenance
Customer: uPVC window extrusion manufacturer
Challenge: Customer needed to proactively maintain their haul off chain to prevent plant downtime.
Solution: By identifying all critical wear parts, we were able to design predictive maintenance kits that made proactive maintenance of the haul off chain as time and cost efficient as possible. These kits are stocked at our local branch and delivered in line with the customer’s predictive maintenance processes.
.webp)
.webp)
Preventative maintenance
Customer: uPVC window extrusion manufacturer
Challenge: Customer needed to proactively maintain their haul off chain to prevent plant downtime.
Solution: By identifying all critical wear parts, we were able to design predictive maintenance kits that made proactive maintenance of the haul off chain as time and cost efficient as possible. These kits are stocked at our local branch and delivered in line with the customer’s predictive maintenance processes.
Preventative maintenance
Customer: uPVC window extrusion manufacturer
Challenge: Customer needed to proactively maintain their haul off chain to prevent plant downtime.
Solution: By identifying all critical wear parts, we were able to design predictive maintenance kits that made proactive maintenance of the haul off chain as time and cost efficient as possible. These kits are stocked at our local branch and delivered in line with the customer’s predictive maintenance processes.
.webp)
Preventative maintenance
Customer: uPVC window extrusion manufacturer
Challenge: Customer needed to proactively maintain their haul off chain to prevent plant downtime.
Solution: By identifying all critical wear parts, we were able to design predictive maintenance kits that made proactive maintenance of the haul off chain as time and cost efficient as possible. These kits are stocked at our local branch and delivered in line with the customer’s predictive maintenance processes.
.webp)
Preventative maintenance
Customer: uPVC window extrusion manufacturer
Challenge: Customer needed to proactively maintain their haul off chain to prevent plant downtime.
Solution: By identifying all critical wear parts, we were able to design predictive maintenance kits that made proactive maintenance of the haul off chain as time and cost efficient as possible. These kits are stocked at our local branch and delivered in line with the customer’s predictive maintenance processes.
Preventative maintenance
Customer: uPVC window extrusion manufacturer
Challenge: Customer needed to proactively maintain their haul off chain to prevent plant downtime.
Solution: By identifying all critical wear parts, we were able to design predictive maintenance kits that made proactive maintenance of the haul off chain as time and cost efficient as possible. These kits are stocked at our local branch and delivered in line with the customer’s predictive maintenance processes.
Customer: uPVC window extrusion manufacturer
Challenge: Customer needed to proactively maintain their haul off chain to prevent plant downtime.
Solution: By identifying all critical wear parts, we were able to design predictive maintenance kits that made proactive maintenance of the haul off chain as time and cost efficient as possible. These kits are stocked at our local branch and delivered in line with the customer’s predictive maintenance processes.
Learn more about Reliability Services
Find out all the ways that our reliability services can help you ensure your business is future-ready.
Preventative maintenance
Working with our major brand manufacturing partners, we are best placed to implement both manual and digital data-driven component, system-specific and whole asset preventative maintenance.
.avif)
Air leak surveys
We can support your engineers in identifying and correcting neglected air leaks in compressor systems. In doing so, we are able to prevent breakdowns, save energy and drive cost efficiencies.
.webp)
Specification upgrades
Using our broad product portfolio, we are able to identify areas of improvement throughout your facility, and recommend specification upgrades that will directly result in cost or energy savings, better operational performance and less downtime.
.webp)
Uptime surveys
Combining a range of our value added services, these surveys take a whole-facility approach to improving uptime. Our recommendations cover all aspects of operation, maintenance and energy usage, and can be tailored to meet specific objectives or to align with your sustainability agenda.
.webp)
Prevent component obsolescence, promote circularity
Extending the operational life of machinery and systems reduces customer reliance on finite materials in line with circular economic principles. By identifying alternatives for obsolete parts, we are able to prevent whole-machine replacements, preserving environmental systems and often improving operational efficiencies at the same time.
.webp)
.avif)
Your technical partner for racking and storage installations
The largest independent provider of industrial components consumables and services in the East Midlands
Our Site Services team are best placed to recommend, plan, erect and inspect racking and storage solutions for any warehouse, storeroom or workshop.
No-obligation audits
For a no-obligation site audit, book a consultation with our Site Services team.
ABCO Site Services
Email: SiteServices@abco.co.uk
Tel: 0115 975 7571
Your technical partner for spill management
The largest independent provider of industrial components consumables and services in the East Midlands
Our Site Services team are best placed to audit, install and maintain a spill management solution that is easy to use and compliant with all relevant UK legislation.
No-obligation audits
For a no-obligation site audit, book a consultation with our Site Services team.
ABCO Site Services
Email: SiteServices@abco.co.uk
Tel: 0115 975 7571